Case Study: Medical Gear Delivered in 17 Business Days
Taurus Engineering delivered a high-precision medical gear molded in Delrin 500P NC010 in just 17 business days, including a full First Article Inspection (FAI) report with all dimensions within spec. A single-cavity Class 102 injection mold with hot tip design enabled quick sampling and approval. The part underwent a full Design for Manufacturability (DFM) process, optimizing it for efficient production with tight tolerances—within 0.001″ of nominal. Every shipment includes ISO 13485 certification, ensuring quality and regulatory compliance for medical applications.
Challenge:
A customer needed a high-precision medical gear, fast.
Solution:
Taurus Engineering delivered production parts in just 17 business days—including full First Article Inspection (FAI) approval and ISO 13485 documentation.
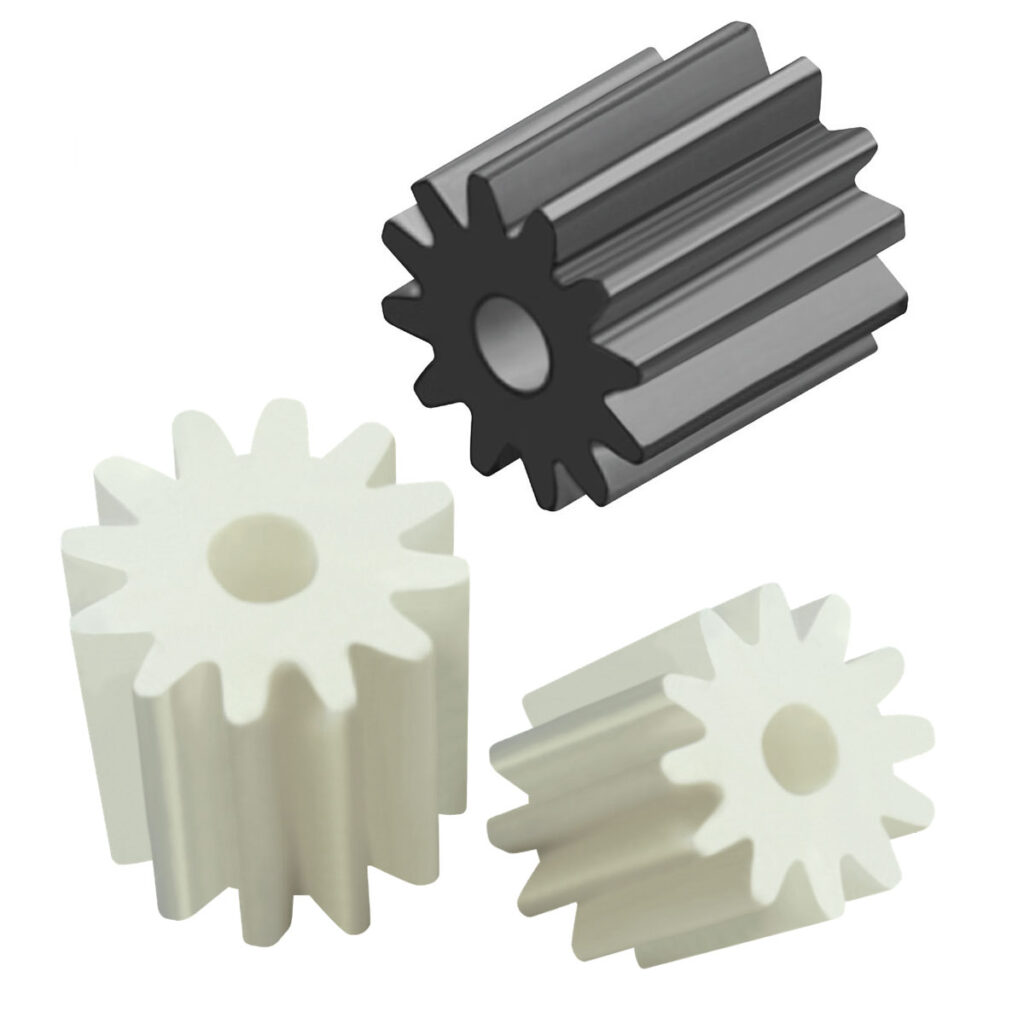
Highlights:
- Material: Delrin® 500P NC010 – ideal for medical use with excellent stability, low friction, and chemical resistance
- Mold Type: Class 102 single-cavity injection mold with hot tip
- Speed: Tool built, sampled, and approved in under 3 weeks
- DFM: Full Design for Manufacturability review ensured smooth production and precision
- Accuracy: All dimensions held within ±0.001"
- Certifications: ISO 13485-certified process for medical compliance
From DFM to production, this project shows how Taurus delivers speed, precision, and quality—even on critical, complex components.