Insert Molding
Insert molding combines two or more components into a single finished part. A pre-manufactured component (e.g., metal or plastic) is placed in the mold cavity, and resin is injected around it to create a unified product. This process eliminates the need for additional assembly and is ideal for complex parts used in medical devices like connectors, infusion sets, IV catheters, valve swivels, and heat exchangers.
Taurus Engineering uses the best molding technique—whether injection, compression, or transfer molding—based on part complexity, production volume, and desired material properties.
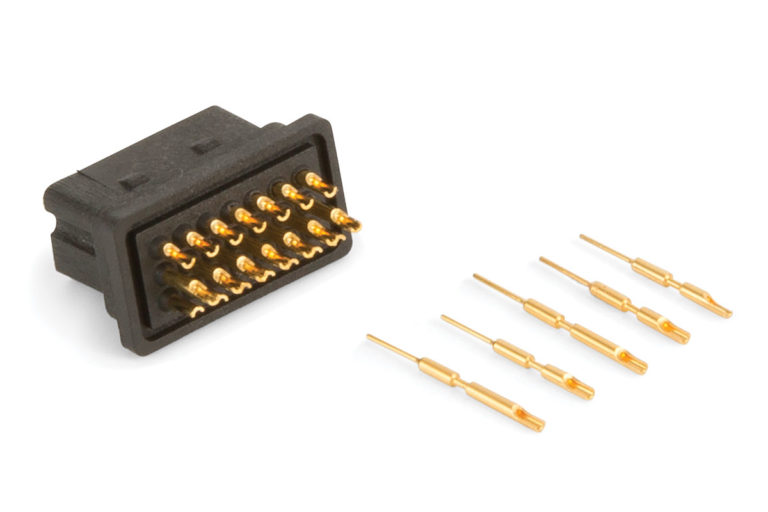
Soft Touch Overmolding
Soft Touch overmolding enhances product design with a soft, rubber-like surface for better grip and comfort. Using thermoplastic elastomer (TPE), we create a seamless bond between soft and rigid materials, improving functionality and durability.
Our process involves molding a substrate (plastic or metal), applying a TPE layer, and curing it to form a strong bond. Benefits include:
- Comfortable, non-slip grip
- Multi-color design options
- Adds flexibility to rigid parts
- Eliminates assembly steps
- Ideal for medical components and devices
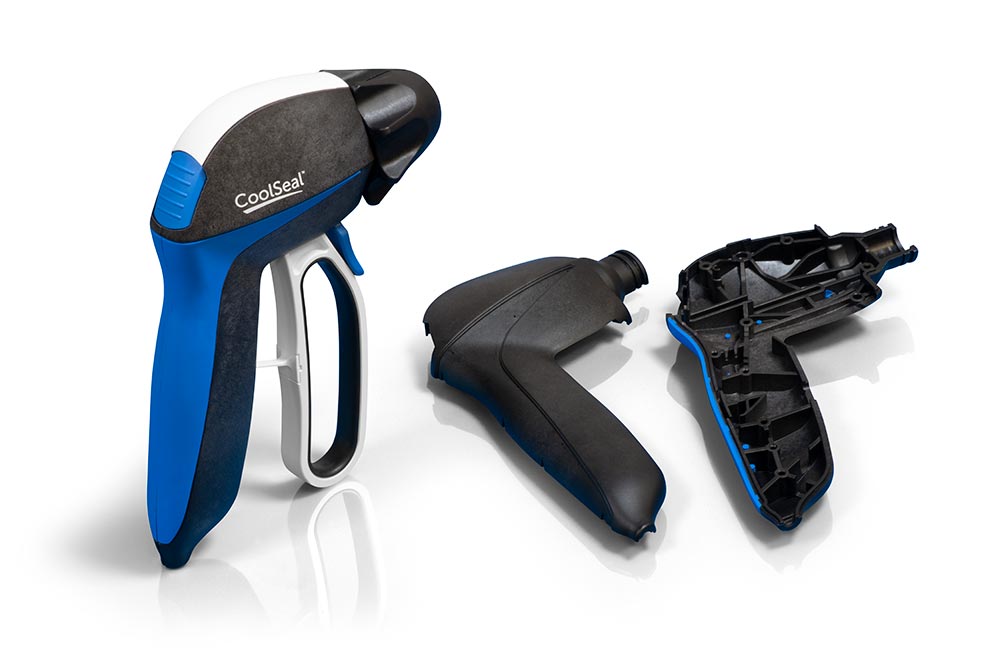
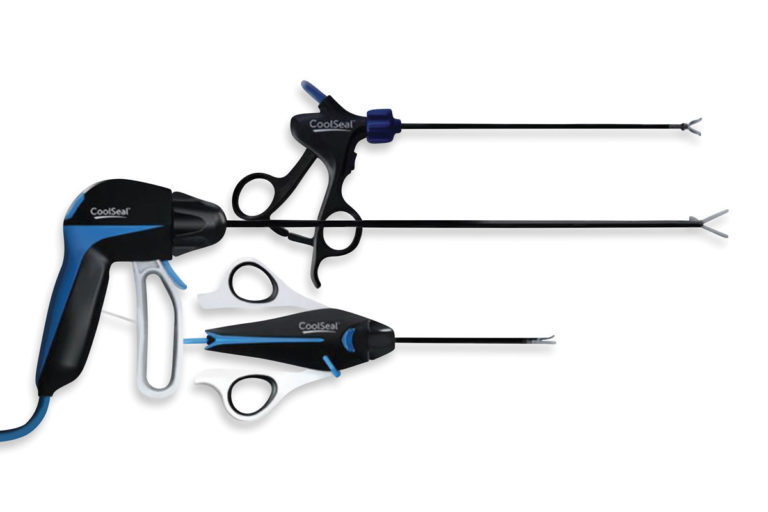